Imagine turning up to a busy Auckland building site. There’s the principal contractor, running the show with the client. Then, in the bustling background, real work happens—by subbies and vendors you probably won’t see promoted on the project board. Lower tier contractors: invisible to most outsiders, but without them, the project would completely grind to a halt. These companies and trades are the backbone of any construction project, plugging the gaps, tackling tasks others pass down the line, and picking up the pieces when things get complicated. But—ask around, and plenty of people in the industry can’t even give a clear definition of what a lower tier contractor is. That’s strange, since these are the folks usually holding power tools, laying cables, or hauling in construction material on a rainy Tuesday. Want to know the ins and outs of how lower tier contractors work? It’s a bit more complicated than the simple labels might suggest.
Understanding Lower Tier Contractors: Who Are They, Really?
In the world of construction, roles get passed like hot potatoes. You start with the client—maybe a developer or company. They hire a main contractor. The main contractor often subcontracts chunks of work—to plumbing specialists, painters, scaffolders, you name it. Those subcontractors, stretched by tight deadlines and chunky contracts, outsource parts again. That’s where a lower tier contractor comes in.
A lower tier contractor is brought onboard by a subcontractor or even another lower tier contractor. Their contract is not with the main client, nor with the primary contractor, but down the pecking order. They could be a flooring installer that works as part of a bigger electrical subcontractor’s crew, or a haulage company moving earth at a landscape team’s request. It’s the supply chain at work—and in construction, this chain gets pretty long. For big commercial builds, it’s not odd to see five, six, or more contract levels below the main job. Each tier passes the buck—and the risk, and the pay—down to the next.
You’ll find lower tier contractors in almost every construction trade. That includes specialists—think of companies who only do waterproofing membranes, glass installation, or high-voltage cable splicing. General labourers often work through agencies that operate at the lower tier level. In New Zealand, an analysis by the Building Research Association in 2022 showed that for every principal contractor, there are on average four levels of subcontracting below on large city projects. The longer the chain, the harder it is to keep track of who’s doing what—and who’s paid.
If you follow the money, you’ll see lower tier contractors don’t just handle construction themselves. They also cover tasks like health and safety plans, on-site waste removal, or dealing with traffic management. They might be responsible for only a specific floor of a building, or one task out of a hundred. Their scope may sound small, but if one slips up, everything above creaks and wobbles. No wonder main contractors now track on-site lower tier crew daily for compliance, safety, and quality reasons.
Stuff gets sticky here: lower tier contractors don’t have direct access to the main contractor or the client for payments, dispute resolution, or safety issues. That puts them at risk—not just with getting paid, but also when information or site instructions aren’t handed down correctly. Most construction disputes and payment delays in New Zealand, according to 2023 numbers from the NZ Building Disputes Tribunal, come from contract breakdowns three or more levels down. That’s where clear documentation and communication gets lost in translation, and small contractors face serious cash flow issues.
So, if you’re running a small subcontracting business, you’ll end up dealing with lower tier contractors. It’s tempting to grab as much help as possible in the hope of beating your own deadlines. But remember—each new contract layer adds complexity and risk. Smart businesses, whether in Hamilton or Whangārei, spend time getting to know who is actually doing the work, how payments will flow, and what risks travel down the chain. Taking shortcuts can blow up a project if one piece at the bottom collapses. Main contractors still hold the real clout, but lower tier subs are usually the first on-site and the last to leave.
Here’s a quick snapshot of how the chain can work:
Tier | Typical Entity | Role/Task Example | Contract Relationship |
---|---|---|---|
Principal Contractor | Main Construction Firm | Overall site management | Directly with client |
First Tier Subcontractor | Large Trades Company | Electrical, plumbing, roofing | With main contractor |
Second Tier Subcontractor | Trade Specialist | Fire alarm install, carpentry | With first tier subbie |
Lower Tier Contractor | Specialist or Labour Hire | Insulation fitting, scaffolding | With second tier or direct subbie |
With every new tier, tracking quality, safety, and payment gets trickier—but projects rely on them at every corner. Understanding this web can save you a heap of time and money.
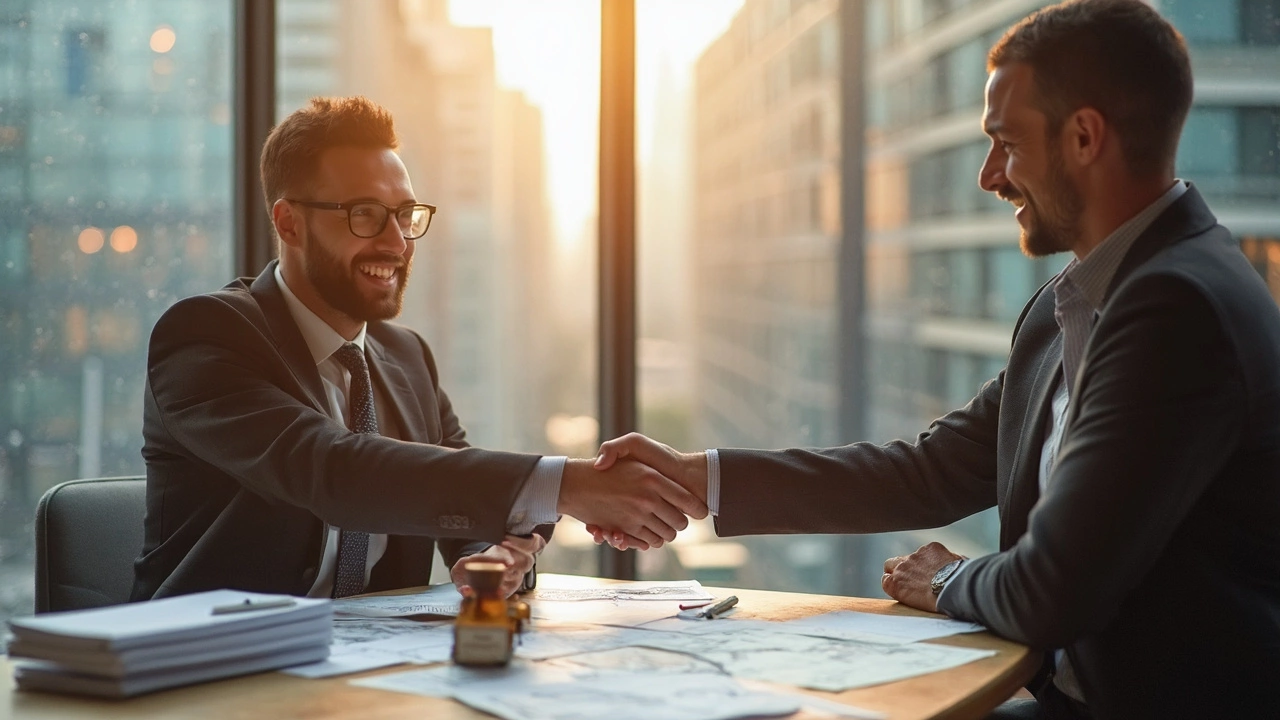
Common Issues and Risks Facing Lower Tier Contractors
Everyone’s chasing the bottom line, but at the lower end of the chain, it’s a rough ride. Payment delays are brutal. Picture this: A painter finishes the job for a second-tier company. The second-tier hasn’t been paid by the first-tier, so the lower tier painter waits. This can spiral for weeks or even months. It’s not just an Auckland thing either—this is a headache that jobs from Christchurch to Wellington share. Data from the Construction Sector Accord (2023) showed average payment times to lower tier contractors in New Zealand stretched past 65 days, compared to the mandated 20 working days for top tier contracts.
This trickle-down—and sometimes freeze—causes problems. Lower tier contractors usually don’t have big reserves or the cash to hold out while bills pile up. You’ll hear stories nearly every week of subcontractors walking off jobs, or even closing shop entirely, when larger companies above them can’t pay or go bust. A firm in Manukau that specialised in laying precast panels had to lay off half its workers last year when its main contractor delayed payments by 90 days. That’s a hard slog.
Then there’s compliance. Main contractors and top-tier subs are tied up with audits, safety standards, and council requirements. But lower tier contractors—especially one-person bands or micro-businesses—often get missed from these processes. They still need to meet health and safety rules, carry insurance, and have their paperwork in line. If they don’t, blame can land anywhere in the chain, but usually piles on those with less leverage. In 2024, Worksafe NZ found that 62% of all construction site safety violations involved staff from third-tier or lower contractors. If you’re hiring work out, you need to check licences, insurance, and safety practices—no matter how temptingly cheap the quote appears.
Communication is another nightmare. Site instructions sometimes come down the line via texts, scribbles on whiteboards, or last-minute emails that get ignored or misunderstood. Major mistakes happen when technical details aren't shared with the people actually doing the task. If the insulation team doesn’t get the new specs for a new eco-product from the architects, you end up with half the building not making energy standards. Suddenly, expensive rework and blame games kick in.
Legal protection is weak. Most lower tier contractors sign contracts heavily weighted in favour of the party above them. Disputes about payment get snagged on “pay when paid” clauses or vague language that can make it hard to enforce your right to get paid promptly. To avoid getting burned, more small subs now use online platforms that keep a clear record of instructions, documents, and changes agreed. Phone calls and handshakes don’t cut it in court if there’s a dispute.
And let’s not forget about reputation risk. If just one lower tier contractor lashes out—maybe cutting corners or tossing rubbish in the wrong pile—it’s not just their name on the line. The whole project’s safety rating or council paperwork can take a hit. That’s why some bigger construction businesses now prequalify all tiers of subcontractors, using national databases or compliance software to weed out fly-by-nighters or uninsured firms.
Here’s what you should keep an eye on if you’re using—or are—lower tier:
- Chase written contracts with crystal-clear terms on payment and work scope
- Insist on seeing certificates, insurance, and site induction sign-offs
- Don’t let tasks or changes drift without a signed variation or clear email
- Ask the party above you to guarantee payment terms by a certain date
- Document everything—not just jobs completed, but instructions you received
- Don’t take on more work than you can safely deliver or delegate
- If in doubt, check with your construction lawyer before signing anything unfamiliar
Contractors who follow those rules tend to get paid faster and stay out of hot water, even when the main contractor is slow to respond. It’s all about risk management.
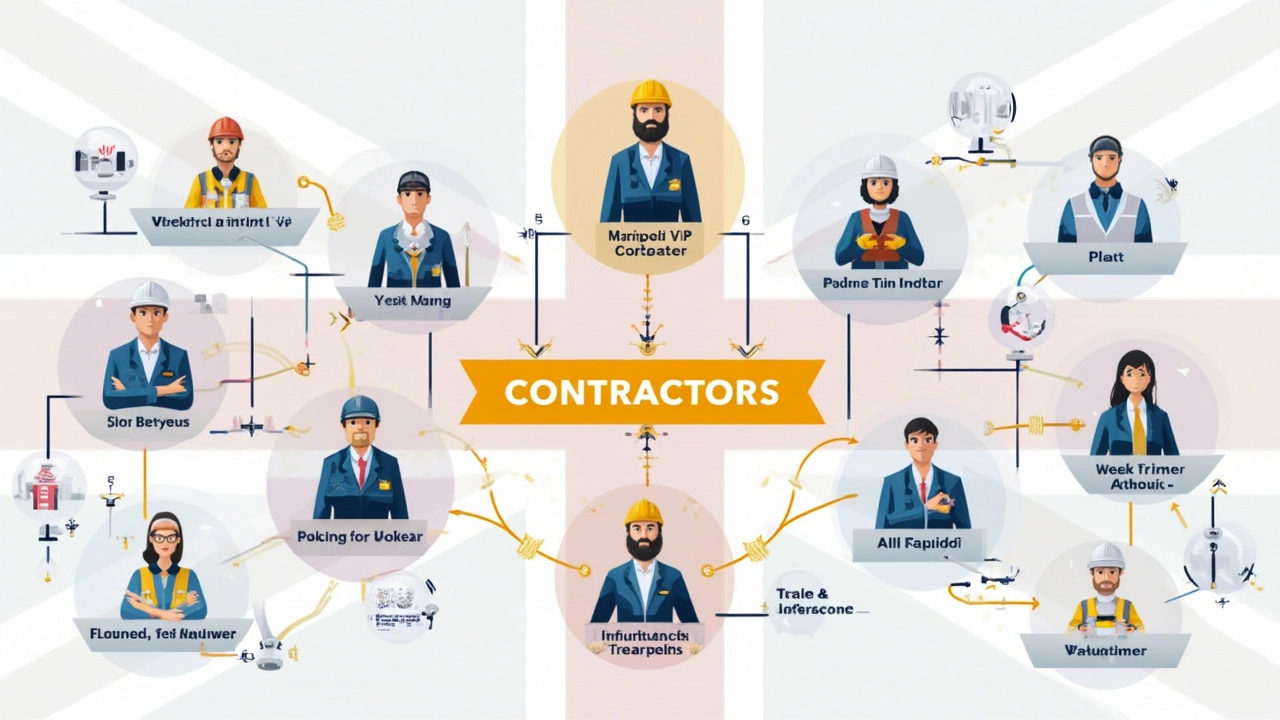
Success Strategies for Working with Lower Tier Contractors
How can you stop headaches before they start? This is where savvy builders and small business owners set themselves apart from the crowd. Start by acting like a project manager and less like a frantic firefighter.
Here’s what top-notch companies do: get a register of every lower tier contractor on your job—right down to the guy running the site hoist or the temporary fencing hire. Building Information Modelling (BIM) software and site apps now help you track not just progress, but who is actually on-site, what their background is, and if their safety training is up-to-date. Nobody wants an unqualified sparky rewiring a high-rise at 5pm.
When it comes to payment, smart companies set up escrow accounts or retentions that protect lower tier suppliers if something goes wrong further up the chain. In New Zealand, construction retentions must legally be held on trust, and the Construction Contracts Act gives even lower tier contractors the right to put in “payment claims” for completed work—don’t wait weeks to send the paperwork!
Training is huge, too. Instead of annual “tick the box” site inductions, leading builders run weekly toolbox talks for all subbies—no matter how many contract levels down—to flag changes, answer questions, and spot risks before they snowball. If everyone in your crew knows the project manager, that’s a sign you’ve fostered a culture where messages don’t get lost. Pulling everyone together in one place (even virtually) builds trust and means they’re quicker to warn about problems or hazards.
Maintaining strong relationships counts for plenty. When Auckland weather grinds projects to a halt, the contractors who get called back—sometimes with little notice—are the ones who proved reliable on smaller jobs before. It makes sense to treat your lower tier crew like partners, not just leftover labour. Shout lunch after a tough pour, say thanks, and pay on time. On my last big job, an electrical subbie’s back-up crew saved us a week by working long hours—because we’d looked after their pay during a slow month. That goodwill is worth more than any fancy contract.
Also, always prepare for disputes. Even with the best paperwork, issues crop up. Have a clear process for mediation or adjudication, and don’t let pride stand in the way. Most payment disputes resolve in weeks if both sides have their documents and communications handy. Avoiding court—unless it’s a lost cause—saves thousands in legal bills.
If you’re an up-and-coming lower tier contractor looking to grow, build your reputation by finishing on time, keeping clean records, and being upfront about problems. Word spreads quickly on big sites, and reliable work attracts better contracts than the lowest quote. Try not to undercut ruthlessly—costing jobs properly and quoting realistic timeframes will get you repeat work that actually makes money.
Finally, be aware: changes in Kiwi law are making things a bit fairer for everyone in construction. Watch out for new legislation around retention money, payment terms, and training compliance. Keeping up with MBIE updates or joining your local Master Builders group will help you stay ahead of new requirements and avoid getting left behind by shifting rules.
Bottom line: lower tier contractors are the unsung heroes and sometimes the biggest risk in our construction ecosystem. If you’re building, renovating, or managing projects in Auckland or beyond, show these contractors respect, keep tabs on documentation, and accept no shortcuts. The project—and everyone’s pay packet—depends on it.