Commercial buildings come in various shapes and structures, each crafted with specific construction methods to meet the demands of different industries. Whether it's a towering skyscraper or a modest retail space, the construction choices can significantly impact functionality and longevity.
In the realm of commercial construction, decisions are often shaped by factors like building purpose, cost, and regional building codes. This article delves into the most common types of construction used for commercial spaces, explaining how each type offers unique benefits and applications. For anyone planning a commercial project, understanding these options can be vital for ensuring the building stands the test of time while serving its intended purpose efficiently.
- Introduction to Commercial Building Construction
- Steel-Framed Structures
- Precast Concrete Buildings
- Wood-Frame Commercial Edifices
- Selecting the Right Construction Type
Introduction to Commercial Building Construction
When the city skyline takes shape against a sunset, or a bustling town square is dotted with grand edifices housing businesses, leisure spots, and offices, it's a testament to the marvels of commercial construction. This sector plays a crucial role in urban development, providing functional and safe structures that accommodate a myriad of activities integral to modern life. The art and science of constructing these robust structures have evolved dramatically over the years, driven by advances in technology, material science, and innovative design philosophies.
Modern commercial building construction is a multifaceted process that begins with an idea and evolves through design and planning stages, implementation, and ultimately to completion. It involves a blend of engineering practices, architectural ingenuity, and strategic project management. The significance of this industry is underscored by the fact that commercial buildings account for a substantial portion of all new constructions globally every year. According to a recent report by the U.S. Census Bureau, commercial construction expenditures in the United States alone surpassed the $90 billion mark in recent years, highlighting the magnitude of this sector in the economy.
The type of construction method selected for a commercial building is pivotal in dictating its future use, aesthetic appeal, and sustainability profile. An effective construction method integrates not just budget and design elements but also considers the environmental impact, energy efficiency, and durability of the building materials. This is paramount as cities worldwide set higher standards for green buildings. For example, a steel-frame structure might be ideal for high-rise offices due to its load-bearing capabilities and speed of erection, whereas precast concrete might be preferred for its fire resistance and acoustic properties in environments like theaters or educational facilities.
"The buildings of tomorrow are being shaped by today's construction techniques, underscoring the need for innovation and sustainability in our urban landscapes." - John Herwitz, renowned urban plannerUnderstanding these nuances is essential for stakeholders ranging from developers and architects to contractors and city planners. They must consider factors like zoning laws, architectural trends, insulation and ventilation needs, as well as technological advancements such as 3D printing and modular construction that are beginning to redefine the industry. Given the complexity and scale of such projects, adopting a collaborative approach where all parties are in alignment with the overarching goal is beneficial for ensuring success and efficiency throughout the lifecycle of the building.
Steel-Framed Structures
The urban landscape and skyline of most major cities owe their iconic silhouettes to steel-framed structures. Dominating the landscape since the late 19th century, this method of construction revolutionized the way we build, enabling the rise of the skyscraper. Steel’s inherent strength and flexibility allow architects and engineers to design buildings that not only reach for the stars but are capable of standing strong against harsh weather conditions and the test of time. Unlike traditional construction methods, steel framing offers a distinct advantage in its ability to span large distances without intermediate supports, creating expansive, open interior spaces that are ideal for commercial activities.
This type of construction involves assembling a skeleton framework of vertical steel columns and horizontal I-beams, which support the floors, roof, and walls of the building. Steel is favored for its unparalleled strength-to-weight ratio, fire resistance, and recyclability, making it an environmentally friendly choice in the era of sustainable building. Tellingly, the construction process for steel-framed structures is more streamlined compared to traditional masonry owing to its pre-engineered components which are fabricated off-site, leading to faster assembly at the construction site. This not only reduces labor costs but minimizes wastage and potential delays, offering significant economic efficiency.
A remarkable example of steel frame architecture is the Empire State Building, which, when completed in 1931, stood as a testament to what could be achieved with this method. As the world moves towards more environmentally sensitive and economically efficient building practices, the use of steel has been a critical component in reducing the carbon footprint of construction projects. In areas prone to earthquakes, steel framing is particularly advantageous, as it provides the structural flexibility needed to absorb and dissipate energy, protecting against catastrophic failures. This resilience is a decisive factor for developers and policymakers tasked with ensuring the safety of urban environments.
Given the strides in technology and modern materials, the commercial construction sector continues to rely heavily on steel-framed structures for practical purposes. The rapid pace of innovation in this area is evidenced by ever-increasing skyscraper heights and more complex architectural designs. According to a 2023 study published by the International Journal of Steel and Cost-efficient Structures, buildings made from steel frames have seen a 30% reduction in energy consumption when combined with modern insulation technologies.
“Steel offers unprecedented versatility while supporting sustainability, and its adaptability makes it indispensable in modern construction,” remarked Dr. Emily Rios, a senior structural engineer and an advocate for green construction practices.
As commercial needs evolve, the ability of steel-framed buildings to adapt through renovations and extensions without significant structural alterations further enhances their value. With urban real estate at a premium, the ability to upgrade rather than replace existing buildings aligns with trends towards economic and environmental efficiency, reinforcing steel framing as a cornerstone of commercial construction. For those embarking on new commercial ventures, considering steel for its durability and adaptability could be a pivotal factor in long-term success.
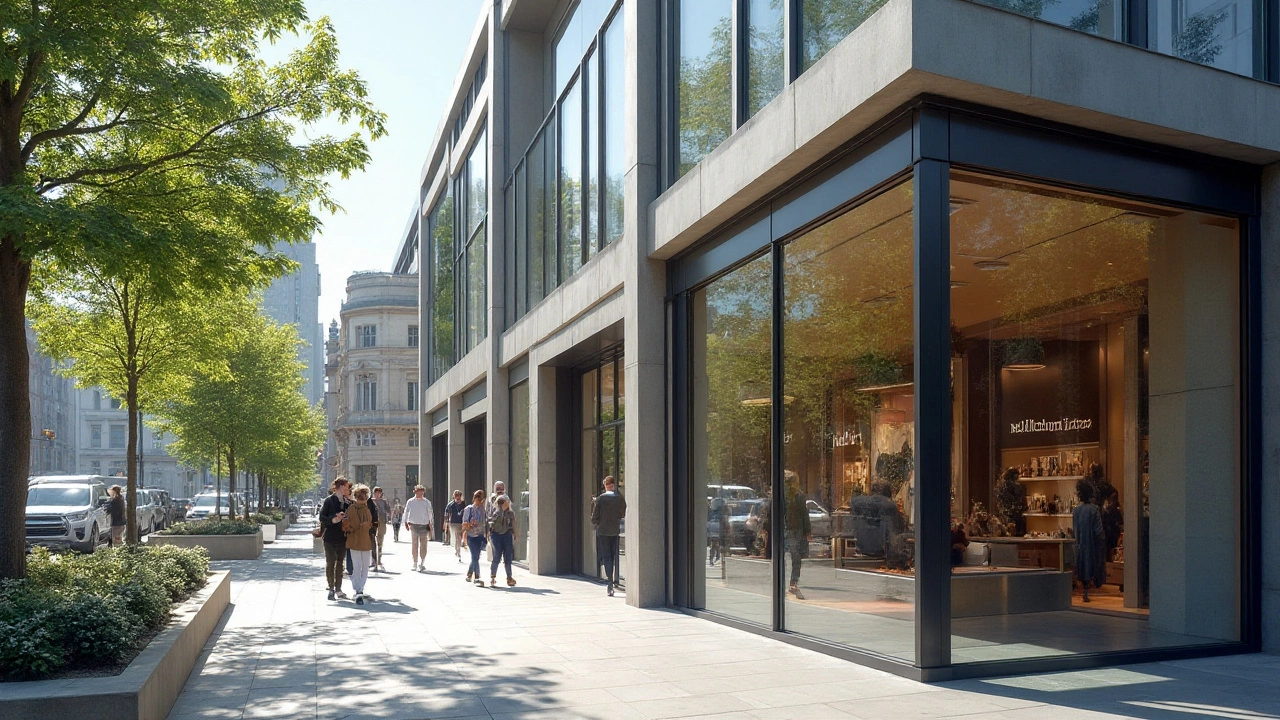
Precast Concrete Buildings
Precast concrete buildings have emerged as a prevalent choice in the commercial building arena, thanks to their durability, versatility, and cost-effectiveness. These buildings utilize concrete elements that are precast, or molded off-site in a controlled environment, and then transported to the construction site for assembly. This method allows for significant quality control, reducing the inconsistencies often encountered with on-site concrete pouring. Another benefit lies in the speed at which projects can be completed; with building components manufactured simultaneously, the on-site assembly can proceed more swiftly, which is particularly advantageous in fast-paced urban environments where timelines are tight.
One of the noteworthy aspects of precast concrete buildings is their enhanced structural integrity. This is due to the precise craftsmanship possible in a factory setting, where factors such as mix consistency and curing environments can be more effectively managed. As a result, precast concrete can withstand a significant amount of stress and strain, making it a preferred choice for earthquake-prone areas. Notably, buildings constructed with precast elements exhibit excellent thermal and acoustic insulation properties due to the density of the material, contributing to reduced energy costs and improved interior comfort levels.
There's also a fascinating environmental angle to consider. The use of precast concrete often results in less waste compared to traditional construction methods. Since exact measurements are used for casting, there's minimal excess material. Additionally, many precasting facilities are committed to recycling waste materials and water used in the production process, reinforcing the environmental benefits. A study conducted by the National Precast Concrete Association highlighted that employing precast methods could reduce construction waste by about 50%, which is significant for projects aiming for green certifications.
Innovations and Applications
In recent years, innovations in precast concrete technology have broadened the application range significantly. Once limited primarily to walls and floors, now entire commercial structures can be built using this method, including shopping centers, office blocks, and more. Designers are increasingly exploring new forms and architectural details, using the adaptability of precast concrete to push creative boundaries. Modern precast construction can also incorporate advanced technology, like built-in insulation and integrated water management systems, which further enhance the building's functionality.
Achieving longevity with such constructions requires a delicate balance between material selection and load considerations. Precast elements come in various thicknesses and reinforcements, making them adaptable to different structural demands. Engineers often collaborate closely with architects to ensure that both aesthetic and structural goals are met. As the construction industry continues to evolve, one exciting direction is the integration of eco-friendly materials into the concrete mix, such as fly ash or silica fume, which improve the sustainability effect without compromising strength. In a surprising nod to precast's versatility, the Seattle Museum of Pop Culture features an exterior primarily made of precast panels, illustrating that functionality and aesthetic appeal can indeed co-exist harmoniously.
"Precast concrete has revolutionized the construction industry, offering unmatched precision and efficiency," notes Dr. Emily Greene, a construction technology researcher at the University of California, Berkeley.
When considering construction methods for your commercial building project, precast concrete offers a compelling blend of benefits that cater to modern demands for speed, safety, and sustainability. There is little doubt that this technique will continue to dominate future trends, driven by innovations that respond directly to the sector's evolving needs.
Wood-Frame Commercial Edifices
The charm and utility of wood-frame commercial edifices have been part and parcel of construction history for centuries. A significant shift from its predominant residential use has emerged, as architects and developers seek sustainable and cost-effective options for commercial purposes. Wood as a construction material is primarily valued for its renewability and lower environmental footprint, making it an appealing choice in an age increasingly conscious of sustainability challenges. Leverage of wood in commercial constructs can vary widely, from local retail shops to broader commercial projects like mid-rise office buildings, which reflects its versatility.
The decision to use wood frames often stems from the material's light weight, which provides easy handling during construction and contributes to faster build times, thereby reducing overall project costs. Wood also offers exceptional thermal insulation properties, contributing to the energy efficiency of a building. Another point of interest is the aesthetic appeal wood imparts, fostering a warm and inviting atmosphere, which is often utilized in hospitality and retail settings. Studies have shown that environments enriched with natural elements like wood can have psychological benefits, promoting a sense of well-being among occupants.
The transition towards wood-frame structures in commercial settings has catalyzed innovative manufacturing techniques and design methodologies. Engineered wood products such as laminated veneer lumber and cross-laminated timber have broadened the horizon for wood, offering strength and durability comparable to traditional building materials. These developments are particularly promising, as they pave the way for wood to be employed in larger-scale commercial buildings with confidence in its load-bearing capabilities and fire resistance. According to a report by WoodWorks, the use of such engineered wood products can significantly decrease construction time by up to 25%.
"From the perspective of sustainability, wood is unparalleled," remarks Sarah Dornberg, an architectural engineer. "When sourced responsibly, wood does more than just contribute to the structural integrity; it plays a pivotal role in reducing carbon footprints while enhancing the aesthetic value of commercial environments."
When considering wood for commercial projects, developers and architects must navigate a matrix of building codes and regulations, especially in regions where seismic and wind loading might be a concern. The American Wood Council provides comprehensive guidelines and standards to ensure that commercial buildings meet safety and performance criteria. An effective strategy involves a balance between traditional insulation approaches and newer methodologies that exploit wood’s natural insulating capabilities, thereby boosting the energy efficiency of a building. As with any construction material, understanding the unique properties of wood, and how it can be integrated into modern commercial spaces, is crucial for optimizing its use.
In conclusion, the rise of wood-frame commercial buildings is emblematic of a broader shift towards sustainability and efficiency in the construction industry. For decision-makers contemplating the adoption of wood in their commercial designs, the plethora of advantages presented by wood, coupled with its environmental benefits, make it a viable and compelling choice. As technology and design in wood continue to advance, it is likely that wood-frame commercial edifices will become an even more prominent feature of urban landscapes around the globe.
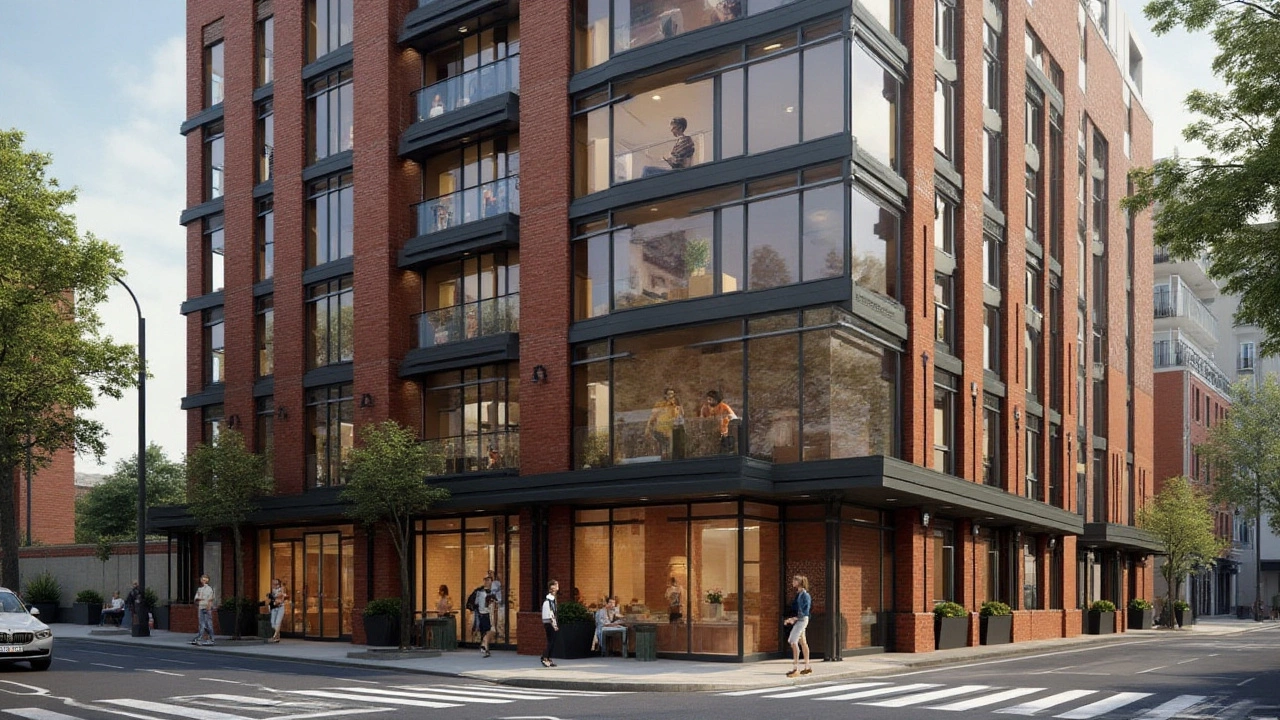
Selecting the Right Construction Type
Choosing the ideal construction type for a commercial building project is a decision that demands careful thought and consideration. What works for a bustling urban office tower might not suit a rural manufacturing plant. The type of construction method greatly impacts not only the cost but also the environmental impact, energy efficiency, and long-term durability of the structure. It is crucial to consult with architectural and construction experts to align the project’s goals with the most effective construction method available. Construction technologies have come a long way, offering materials and techniques that can almost seem futuristic. These advancements allow for more flexible designs, increased durability, and sometimes, faster construction times.
One significant factor to consider is the intended use of the building. For instance, steel-framed structures are optimal for high-rise office buildings because they are sturdy and can withstand various forces, like wind or earthquakes. On the other hand, for smaller commercial buildings like retail stores, precast concrete offers an efficient solution due to its cost-effectiveness and energy efficiency. The environment and climate where the building will be located also play a critical role. Timber might be favored in regions with abundant forest resources, providing a sustainable option, although not everyone is keen on using timber due to concerns about fire risks. Meanwhile, cold climates might find masonry better suited due to its thermal mass, keeping interiors warm during harsh winters.
Budget considerations can't be overlooked either. Different construction types often have different initial costs and upkeep expenses. Steel, while sometimes more expensive upfront due to the need for precise engineering and skilled labor, can prove cost-effective in the long run due to its durability and low maintenance requirements. In contrast, a wood-frame structure might be cheaper to erect but could potentially incur higher maintenance costs over its lifetime, especially in areas prone to pest or moisture exposure. Additionally, local regulations and permits can affect the decision, as some areas have restrictions based on environmental impact or aesthetic guidelines, potentially limiting material choices.
Moreover, the speed of construction might be a deciding factor, especially for projects with tight deadlines. Precast concrete elements, for example, can dramatically cut down on construction time because they are manufactured off-site and assembled quickly on location. This method not only speeds up the building process but also minimizes labor costs and site disruption. Conversely, traditional masonry or on-site concrete pouring can be more labor-intensive and time-consuming, but they might yield a more customizable finished product. As technology evolves, more construction firms are turning to innovative solutions like 3D printing for certain building components, showcasing the array of options at a project manager's disposal today.
The American Institute of Architects recommends "evaluating each construction method's long-term performance record in similar applications," highlighting the importance of data-driven decisions.
Finally, sustainability is a growing consideration with the rising awareness of our environmental footprint. Certain construction types are inherently more sustainable; for example, timber has the lowest carbon footprint among all building materials if sustainably sourced and managed. Steel and concrete companies are also making strides in recycling efforts, ensuring that materials used are from recycled sources where possible, which benefits both sustainability and public relations aspects of a commercial project. As businesses and society at large push for greener practices, opting for a construction type that aligns with these values can provide competitive advantages and fulfill corporate social responsibility objectives.